Common Applications of Chemical Defoamer Across Multiple Fields
Common Applications of Chemical Defoamer Across Multiple Fields
Blog Article
The Importance of Making Use Of a Chemical Defoamer in Various Applications
The application of chemical defoamers is a crucial consideration throughout numerous markets, including food handling, wastewater treatment, and pharmaceuticals. These representatives play an essential role in mitigating foam formation, which can impede performance and concession product high quality.
Recognizing Foam Development
Foam development is a complicated physical phenomenon that happens when gas bubbles are caught within a fluid matrix, resulting in the production of a stable structure. This process can be affected by different factors, consisting of the viscosity of the fluid, the surface area stress at the gas-liquid interface, and the presence of surfactants. Surfactants reduced the surface stress, promoting bubble production and stabilization, which often leads to the development of foam in numerous industrial procedures.
Foams are frequently encountered in applications such as food manufacturing, wastewater treatment, and chemical production. In these contexts, foam can act as an insulator, hinder blending processes, or impede the efficiency of tools. The stability of foam is identified by the balance in between the forces acting to stabilize the bubbles and those that promote their collapse.
Recognizing the mechanics of foam formation is essential for successfully handling its existence in numerous systems. By understanding the underlying concepts, sectors can develop strategies to reduce undesirable lathering, thus boosting operational effectiveness and item top quality. This foundational understanding serves as a precursor to checking out the utility of chemical defoamers, which especially address foam-related difficulties in many applications.
Advantages of Chemical Defoamers
Chemical defoamers provide considerable benefits throughout various industries by successfully managing and minimizing foam development. Among the key benefits is enhanced operational effectiveness. By lessening foam, chemical defoamers aid maintain ideal manufacturing prices and lower downtime associated with foam management. This is specifically important in procedures where extreme foam can restrain equipment or disrupt process.
Furthermore, chemical defoamers add to boosted item high quality. Lathering typically results in variances in solutions, which can adversely influence the final product. By regulating foam degrees, defoamers guarantee uniformity, thus boosting the total high quality of the outcome.
Cost-effectiveness is another remarkable benefit (Chemical Defoamer). By lowering the amount of resources needed for manufacturing and reducing waste, chemical defoamers can result in significant financial savings. In addition, they commonly permit minimized power usage, as processes can run more efficiently and require less intervention.
Applications in Food Processing
In the food processing sector, efficient management of foam is crucial to guarantee both item high quality and operational effectiveness. Foam can disrupt numerous processes, from mixing and mixing to packaging, bring about reduced returns and prospective contamination. Chemical defoamers play an essential function in minimizing these issues by promptly breaking down foam, allowing for smoother operations and improved product consistency.
In applications such as milk processing, defoamers prevent excess foam development throughout the production of cheese, yogurt, and milk, which can interrupt equipment and influence the texture of the end product. In brewing and fermentation processes, foam control is crucial to keep the integrity of the beverage and make certain optimal fermentation rates.
Additionally, chemical defoamers are used in food dressings, solutions, and sauces to boost the stability and look of the last items. By minimizing foam during production, manufacturers can attain better mixing and dispersion of active ingredients, causing superior quality. In general, the consolidation of chemical defoamers in food handling is crucial for keeping efficiency, top quality, and safety and security in food production.
Role in Wastewater Therapy
Effective foam management is equally essential in wastewater treatment processes, where excessive foam can impede operations and complicate the treatment of effluents. In numerous wastewater treatment centers, foam can form as a result of organic task, surfactants, or various other natural products existing in the influent. This foam can lead to a series of operational challenges, consisting of reduced therapy efficiency, enhanced maintenance requirements, and potential regulatory compliance concerns.
Chemical defoamers play a critical duty in minimizing these obstacles. By minimizing the surface stress of the fluid, defoamers promote the collapse of foam structures, thus facilitating smoother procedure of tools such as oygenation containers and clarifiers. Their prompt application assists preserve optimal hydraulic problems, boosting the general efficiency of solids splitting up processes.
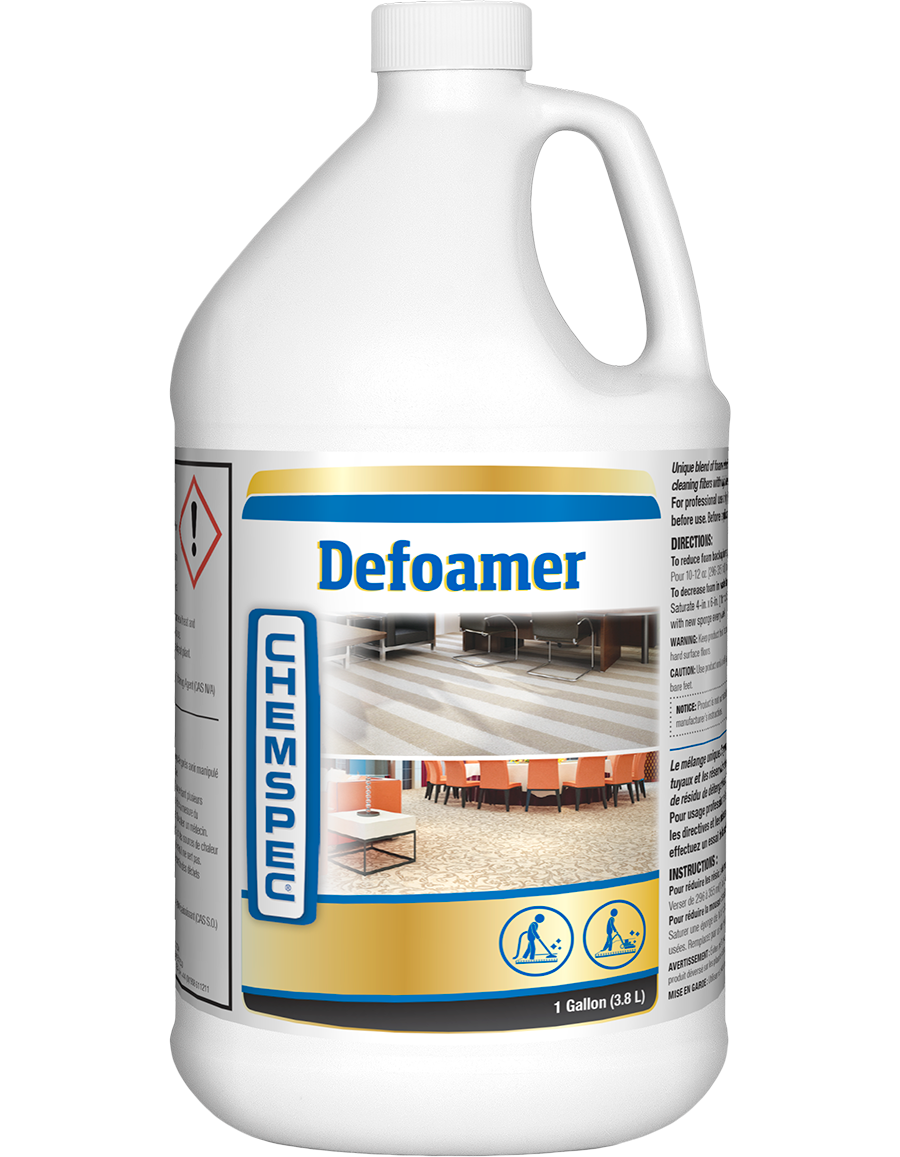
Effect on Pharmaceutical Manufacturing
Foam control is essential in pharmaceutical production, where the presence of excessive foam can disrupt manufacturing processes and concession item high quality (Chemical Defoamer). The development of foam throughout different phases, such as blending, blending, and fermentation, can lead to inefficient blending, insufficient warm transfer, and even devices damage. These issues not just lead to functional delays but can also cause substantial financial losses and impact compliance with check my reference stringent governing criteria
Chemical defoamers are specifically formulated to reduce these challenges. By effectively reducing foam development, they improve procedure effectiveness and keep the stability of the end product. In certain, defoamers make sure consistent dose kinds, enhance the stability of suspensions and solutions, and simplify cleaning processes by avoiding foam accumulation in tools.
Additionally, making use of defoamers can maximize the yield of energetic pharmaceutical ingredients (APIs) by promoting far better removal and purification procedures. As pharmaceutical companies make every effort to enhance product quality while lessening production prices, the function of chemical defoamers ends up being progressively vital - Chemical Defoamer. Their consolidation into making protocols not only sustains compliance with Excellent Manufacturing Practices (GMP) yet likewise cultivates innovation and competition in a rapidly progressing industry
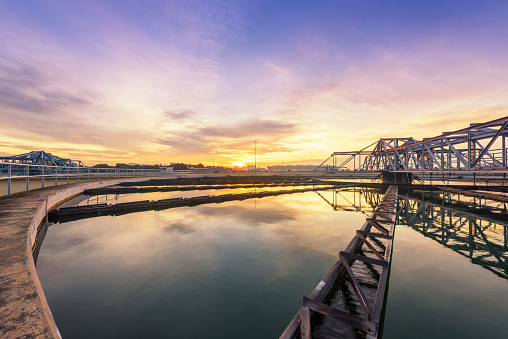
Final Thought

Chemical defoamers use significant benefits across different industries by properly decreasing and managing foam formation. By lessening foam, chemical defoamers help Look At This preserve ideal production prices and reduce downtime linked with foam management. Chemical defoamers play an essential duty in alleviating these issues by rapidly damaging down foam, permitting for smoother operations and improved item uniformity.
Effective foam monitoring is equally important in wastewater therapy procedures, where excessive foam can impede procedures and make complex the therapy of effluents.Foam control is essential in pharmaceutical manufacturing, where the presence of excessive foam can interrupt making procedures and concession item quality.
Report this page